Was MLB's Juiced Era Actually A Juiced-Ball Era?
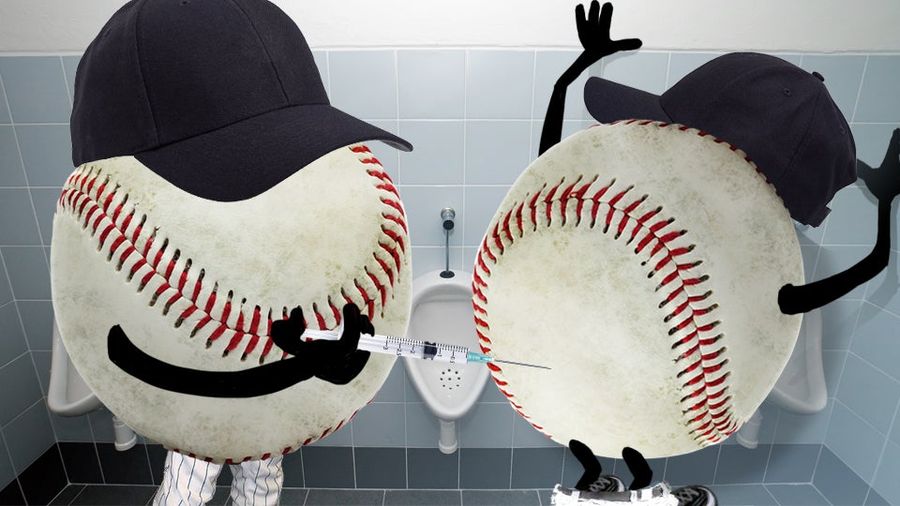
The following is adapted from a chapter of Extra Innings, a collection of incisive and mythbusting essays from our friends at Baseball Prospectus.
Perhaps more than any other culprit, "juiced" baseballs could explain the rise in home runs during the Steroid Era. Unfortunately, much of the evidence for changes in the ball is indirect, accompanied by a generous helping of anecdotes, and cloaked in perennial denials from manufacturers and other officials. Still, unraveling the truth about what may have changed inside the baseballs—and how those changes could have contributed to the home-run boom—isn't an impossible task given enough patience to sift through the literature on the topic.
Recall that the switch from Spalding to Rawlings as the supplier of major league balls in 1977 coincided with a 50 percent jump in home runs across the two leagues. The 1977 rates weren't unprecedented; both leagues had been at similar heights as recently as 1970, itself a spike year for homers. The 1976 rate of 0.58 homers per game was the lowest since 1946, even lower than 1968. Prior to the switch in manufacturer, the last major change to the ball had come in 1974, when the outer coating switched from horsehide to cowhide because of a shortage of the former. Homer production fell from 0.80 per game to 0.68, a 14.7 percent drop. It increased 2.4 percent in 1975, but then fell off another 17.4 percent in 1976.
Given those ups and downs, it's possible that Spalding didn't perfect the process of using the new covering before surrendering the manufacturing process to Rawlings, or that the balls used at the end of their run were leftovers that were slightly substandard in resilience, leading to the dip in home runs. It would take a Deep Throat to provide insight into the matter, but unlike in the Watergate scandal of that decade, none has ever come forward. In any event, aside from 1976, the rises and falls around that time fit right in with the garden-variety season-to-season variation in the expansion era.
Here it's worth reviewing the composition and construction process of a major league baseball. The ball starts as a pill of cushion cork (a mixture of cork and ground rubber) of prescribed weight (0.50 ounce) and diameter (2.86 to 2.94 inches). The pill is then wrapped in two layers of rubber, one black and one red, bringing the weight to 0.85 (+/-0.05) ounce and the diameter to 1.375 (+/-0.01) inches. After that, the sphere is tightly wrapped with three layers (166 yards) of wool yarn and one layer (150 yards) of cotton-polyester yarn. The materials are important. Wool's natural resiliency and "memory" allows it to rapidly return to its original shape after being struck, while the cotton-poly blend reduces the risk of tears when the cowhide is applied. The balls are measured for size, weight, and tension after each layer to ensure that they fall within similarly tight tolerances.
The wound ball is trimmed of excess tailings, coated with a layer of latex adhesive, and then surrounded by the familiar two pieces of leather, which are hand-sewn together with 88 inches and 108 stitches worth of waxed red thread. After stitching, the balls are machine-rolled to compress the seams, dried in a dehumidifier, and rolled again before being cosmetically graded to check for abrasions and blemishes. They are then measured and weighed again. To meet official specifications, balls must measure 9 to 9.25 inches in circumference across two seams, and weigh from 5 to 5.25 ounces. From there they are stamped, weighed, inspected again, and then hand-packed for shipping.
After they arrive at a central warehouse, approximately 28 out of every 10,000 balls are run through tests. The balls are shot out of a pitching machine at 85 feet per second into a board of northern white ash (the same as used in the majority of bats), with its speed coming off the board measured to determine its coefficient of restitution. Balls must have a coefficient of restitution between .514 and .578, meaning that they must rebound at between 43.69 and 49.13 feet per second to meet standards.
Note that at every stage, some amount of tolerance is allowed, an amount that is hardly trivial. In 2000, as balls were flying out of the park at record rates, Major League Baseball and Rawlings funded a study at the University of Massachusetts-Lowell Baseball Research Center; there a team of mechanical engineers led by Prof. Jim Sherwood put 192 unused 1999- and 2000-vintage balls through a battery of tests and accompanied MLB personnel on tours of the plants where various components were manufactured, issuing a 28-page report on their findings. The tests "revealed no significant performance differences and verified that the baseballs used in Major League games meet performance specifications." Yet they also found that "some of the internal components of the dissected samples were slightly out of tolerance on baseballs from each year … despite the thorough inspection process in place at the assembly plant in Costa Rica." Thirteen out of the 192 baseballs supplied (6.8 percent) were underweight as well.
The most glaring finding was the effect of the tolerances. According to the study, "two baseballs could meet MLB specifications for construction but one ball could be theoretically hit 49.1 feet further," which breaks down to 8.4 feet attributable to being on the light side of the tolerance for weight (5.0 ounces, as opposed to 5.25 ounces) and another 40.4 feet attributable to being on the high end for the coefficient of restitution (.578). Given that finding, it's not difficult to imagine how the slightest differences in the balls from batch to batch or year to year could lead to a plethora of towering 425-foot home runs instead of 375-foot warning track fly balls. The researchers also noted that minor league balls, with pure cork centers (as opposed to cushion cork, which contains ground rubber), didn't fly quite as far, a shortfall of about eight feet, illustrating how minor changes in the core can manifest themselves on one side of the warning track or the other.
In addition, a test sponsored by the Cleveland Plain Dealer that didn't use aged baseballs drew some interesting results. Using baseballs from 1999 and 2000, engineers at the Lansmont Corporation in Silicon Valley replicated National Bureau of Standards liveliness tests that had been done in 1945, and found that the big-league balls sampled could fly up to 48 feet farther than their counterparts, which hailed from 1942.
At the time of this wave of testing, the common refrain from Rawlings was that since 1931 there had been no changes in specifications for the balls outside of humidity and temperature controls, improved quality control, and testing. That 1931 date corresponds to the introduction of the cushion cork pill, following the two highest-scoring seasons in the history of post-1900 baseball (5.19 and 5.55 runs per game in 1929 and 1930, respectively); prior to that, the ball had had a pure cork center.
Even so, a close look at the UMass-Lowell report—which in addition to detailing the official specifications of the ball, covered the sourcing and construction of the cork and rubber used in the pill, the wool used in the winding, and cowhide used in the cover—reveals gaps, discrepancies, and hints of change over the years. Perhaps the most notable omission from discussion is the presence of a red ring used in the assembly of the pill, unaccounted for in the specs. The ring sits between the hemispheres of black rubber that encase the cushion cork sphere; in the report, it is referred to as a hard red-rubber washer sliced from a hard red-rubber tube, made at the same Mississippi facility as the rest of the ball's rubber components, but whereas those pieces are meticulously documented as to their content, the washer, though photographed as a separate item and as part of a partially assembled pill prior to being encased in the red layer, is not otherwise mentioned anywhere in the report.
Fast-forward to January 2007, when a diagnostic imaging company called Universal Medical Systems (UMS), with assistance from scientists from the Center for Quantitative Imaging at Penn State, examined the ball hit by Mark McGwire for his 70th home run in 1998 via computerized tomography (CT) scans. The scans clearly showed the presence of the ring, leading the scientists to conclude that the ball was juiced. Said UMS president David Zavagno, "The synthetic rubber ring of the modern-day baseball, in this case that of Mark McGwire's prized 70th home run ball, acts as both a spring and a 'stop' ... Much like a sling shot pulled back 10 or 20 degrees farther than normal, the subsequent restitution or rebound allows an object to fly faster and farther. The changes to the center directly affect the restitution and energy distribution within the ball."
MLB spokesman Rich Levin claimed that the ring was more like "a cardboard washer." He did not elaborate on that absurd explanation, but Bob Dupuy, MLB's chief operating officer, carefully refuted the imagers' claims. "All of our balls are subject to rigorous quality control standards and testing conducted by Rawlings," he said. "No changes have been made to the core of the ball through the entire time they have manufactured it. We are satisfied that the ball comports with all major league specifications." Dupuy noted that annual tests were still being conducted at UMass-Lowell under Sherwood's direction.
Shortly after the UMass-Lowell report came out, a team of University of Rhode Island (URI) forensic scientists led by Dennis Hilliard solicited the donation of foul balls via a radio station for the purposes of testing. They obtained only a handful, one apiece from 1963, 1970, 1989, 1995, and 2000, which limited any claims as to statistical significance produced by their coefficient of restitution tests (reportedly, the two newest pills rebounded about 30 percent higher), but their examinations of the balls contrasted with the report as well as Rawlings's claim.
Using infrared spectroscopy and digital photography, the URI team determined that the 2000 pill was similar in color to the 1985 and 1999 pills. However, they also noted that "the design is unique among all years with a larger space between the two black rubber hemispheres." Furthermore, the team's findings with regard to the yarn were at odds with the UMass-Lowell report, particularly when they performed their own bleaching to measure the non-wool content. (The method is simple: The bleach dissolves the wool. Whatever's left over isn't wool.) Here's Discover Magazine:
As expected, the yarn from the 1963 ball dissolved completely, as the bleach ate away the protein in the wool. But when the 1970 sample was tested, trace amounts of synthetic fibers remained, and with the 1989, 1995, and 2000 balls, "the fibers were pretty much still intact," [textile scientist Linda] Welters says.
Preliminary tests found as much as 21.6 percent synthetic fiber in the yarns from the 2000 ball, thus falling outside the 15±3 percent tolerance detailed in the UMass-Lowell report. The URI scientists were at odds with the manufacturer over such matters:
"My guess would be that they're somehow getting a lot of polyester mulched into the mix, since it's very hard to find all-wool carpets being made these days," Welters says. Paul Dubin strenuously disagrees. He says his company tests the yarn every day to ensure that it is within Major League guidelines.
Back to Zavagno, who made headlines again in 2007 when he alleged that contemporary (Bonds-era) baseballs differed materially from "traditional" (Aaron-era) balls from earlier decades:
In 1999, one year after Mark McGwire broke the single-season home run record, the League decided to remove the timeless imprint "cushioned cork center" from official baseballs, according to David Zavagno, president of UMS, a worldwide innovator of diagnostic imaging technology for various industries.
"The League decided to juice itself so they pumped the new ball into their system . . . By examining the CT images of Bonds-era baseballs, you can see the ball has been upgraded to include a rubberized pill, the addition of polyester in the windings and a very hard synthetic ring or spring. As the CT images demonstrate, the League apparently allowed the composition of the baseball to further change from 1998 to 2001 destroying the integrity of the game's statistics, including home run records."
Zavagno was mistaken in claiming that the pill was suddenly "rubberized," since rubber had been part of the cushion cork mix since 1931. Nonetheless, a side-by-side comparison of the CT scans he presented did illustrate density differences between the otherwise undated Aaron- and Bonds-era balls, both with regard to the pill and the yarn. Beyond the knowledge that the former is a Spalding-made ball (Aaron retired in 1976, Spalding's final year as supplier) and that the yarn may have been hand-wound instead of machine-wound (it's unclear exactly when the switch was made), the significance of this is unclear, as there's no way to know under what conditions—particularly with regard to heat and moisture—the older ball was stored. The scan of the older ball does show an analogous rubber ring, smaller and less dense than its modern-day counterpart.
Physicist Alan Nathan is among those who believe that the ball has changed. Nathan, whose credentials include chairing the Society for Baseball Research's Baseball & Science Committee and serving on a scientific panel advising the NCAA on issues related to bat performance, is quite familiar with Sherwood's study and his laboratory, having served as part of a scientific advisory committee for a 2002 study of bats (more about which below) that was done at the Lowell lab.
Of the Zavagno scans, Nathan says, "What he shows is that the construction of baseballs has changed. There's no question that the construction has changed, the pill has changed, the percentage of wool in the windings has changed, some of it's synthetic now. There are structural differences between the baseballs." In Nathan's eye, showing that isn't enough. "Structural changes do not necessarily imply performance changes."
To the extent that COR tests for balls of different vintages have been made public via means like the UMass-Lowell, Plain Dealer, or Nathan's work with fellow physicist Lloyd Smith, they have shown relatively little difference among small batches of balls obtained via a minimal number of sources. Even so, it's important to remember just how wide MLB's tolerances are. Says Nathan, "The specs on major league baseballs, they almost don't deserve to be called specs, they're so loose that the range of performance from the top end to the bottom end is so different."
Indeed. The 49.1-foot discrepancy in flight for two balls at the extremes of tolerance is roughly three times the distance produced by a three percent increase in batted ball speed. That's according to the rule of thumb cited by Nathan in his evaluation of data on home run distances, whereby each additional mile per hour of batted ball speed increases the fly ball distance by 5.5 feet. That's a lot of extra homers added to the ledger without anyone violating the rules.
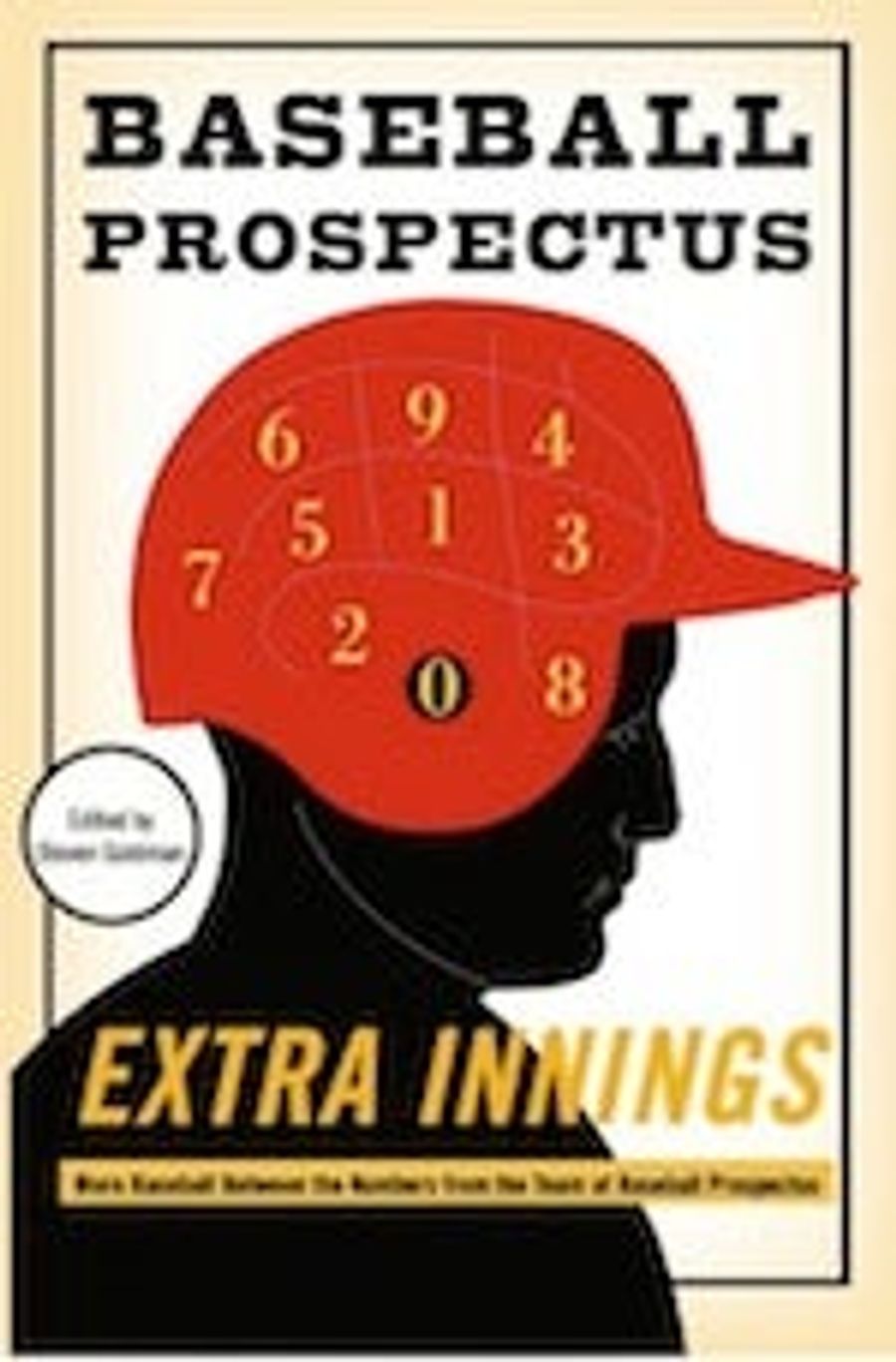
Adapted from "What Really Happened in the Juiced Era?" by Jay Jaffe, a selection from Extra Innings: More Baseball Between the Numbers from the Team at Baseball Prospectus, ed. Steven Goldman (Basic Books, 2012). Top image by Jim Cooke.
Related
Monday’s MLB Best Bets: August 11th Top Baseball Picks
Can Tommy Fleetwood Finally Break His PGA Tour Drought?
WNBA Officiating Under Fire as Stars Demand Change
MLB Best Bets Friday August 8th: Top Betting Picks Today
- Best NFL Preseason Bets for August 8th: Friday Preseason Top Picks
- MLB Best Bets Friday August 8th: Top Betting Picks Today
- NFL Preseason Week 1 Picks: Best Bets for Thursday August 7th's Slate
- Three Overlooked College Football Playoff Long Shots Worth a Bet
- Wednesday MLB Picks: August 6th Top Baseball Betting Predictions
- Top MLB Home Run Prop Picks for Tuesday: Best Bets for August 5th
- MLB Best Bets Today: Monday August 4th Baseball Top Betting Picks